Our history
Dylog Hitech was established/founded as a spin-off of the high-tech branch of the Dylog S.p.A. Group, one of the main players in the Italian Information Technology market.
Years of experience
in the inspection of food products and packaging and in threat detection in the security sector, Dylog Hitech aims to provide a comprehensive range of turnkey products that combine ease of use, low cost of ownership, and flexibility in implementing custom solutions for the most demanding customers.
Our mission
A goal since 1996
Since 1996, our technology has been aimed at minimizing the level of risk deriving both from the contamination or non-compliance of food products, dangerous for the health of consumers, and from threats to the safety of the population, mainly through the control of baggage and packages.
Proprietary technology
Dylog Hitech manages and develops all its technologies internally, investing heavily in innovation in both the hardware and software fields, with an eye on sustainability. This has always been the distinctive feature of a constantly growing company, also thanks to the support of a large group such as Dylog/Buffetti.
Hardware and Software costumization
An internal team of engineers take scare of hw and sw to guarantee the constant enhancement of our machines’’ functionality.
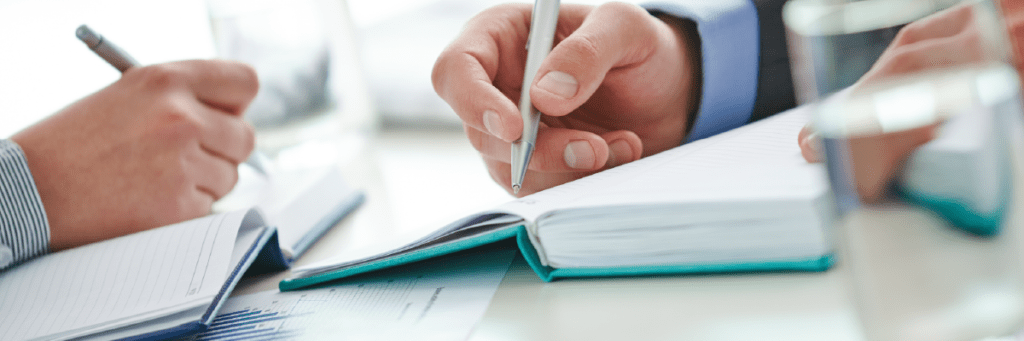
Remote Service
We offer a remote support service allowing us to get connected to our customers’ machine son site and solve any issues which does not require the repleancement of components.
Training
We schedule offer training sessions on our machines (different levels: Operator, Supervisor, Maintainer, etc.) in order to make sure that our customers can work safely without our continuous support.
Extraordinary Assistance
We support our customers intervene to resolve unexpected machine breakdowns, avoiding production stops.
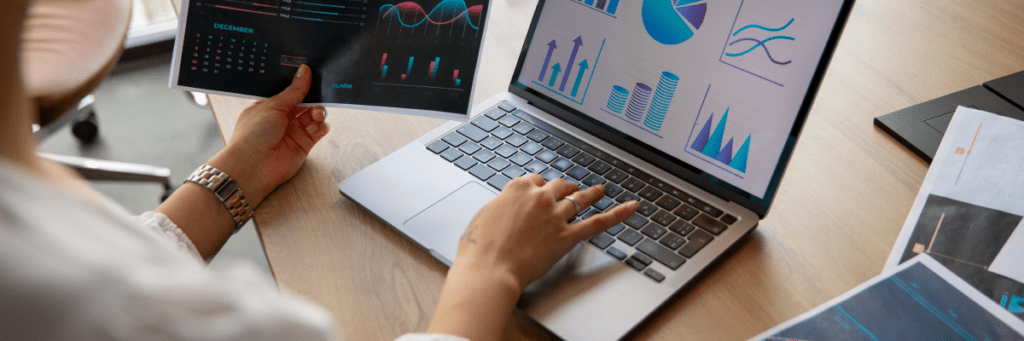
Sample check and Batch Reworking
We propose this service on site (also send an engineer for the machine setup) or getting the product batches to be reworked at our premises. In both cases, we submit a final quality control report.
Preventive Assistance and Performance Validation
We schedule on-site visits to check that the machine is working properly and intervene to replace any worn parts before damage occurs, as well as checking that the software reads contaminants correctly.
Software and Settings Update
Software and update management, creation of dedicated setups for new products, installation and configuration of new tools and customizations.